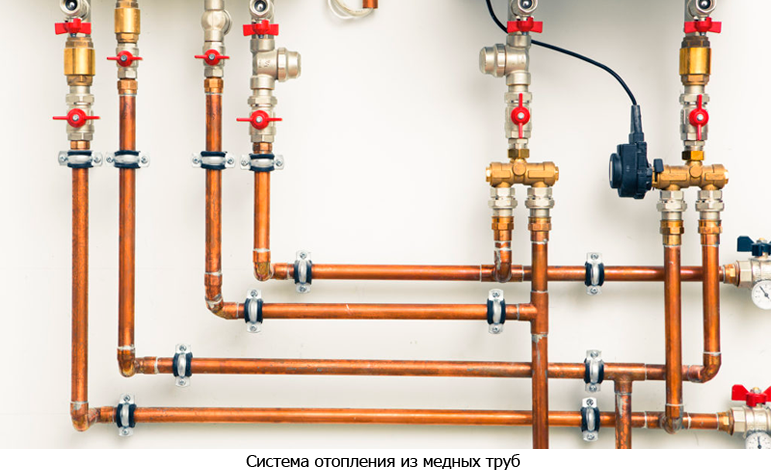
Types of pipes and ways to connect them
For installation of internal water supply and heating systems, pipes made of steel, copper, metal or plastic are used. Today, steel pipelines are considered obsolete. More often choose copper, metal-plastic or polypropylene pipes. You can install the structure on your own, without involving experienced installers.
The characteristics of materials require different methods for pairing of pipes and certain types of fittings are additional items. There are such types of fittings as transitions, tees, bends, corners, couplings, etc. Pipes of equal cross-section are fastened with straight fittings, of different cross - sections-with transitional ones. According to the method of fastening, there are threaded, clamping, and press fittings. There is also a spike for welding. For household structures, use fittings that are attached with a thread.
If you plan to use plastic pipes, you should carefully monitor their quality when buying:
• the product must have a strictly circular cross-section both outside and inside;
• the wall thickness of straight sections and transitions must be the same on all elements and along the entire circumference;
• the surface of the products must be smooth and smooth, without any flaws;
* the elements must be connected to each other with difficulty and only in a heated form.
Attachments are important parts of the device. They allow you to warm up the solid material and give it plasticity, after which the elements to be joined will be firmly and hermetically connected. Structurally, the nozzle consists of two separate elements (mandrel and sleeve), fixed to the heater from different sides with a chrome bolt. To avoid sticking of the softened plastic to the nozzles, they are covered with a layer of Teflon, which has a blue or gray color. Each pair of nozzles corresponds to one of the pipe sizes.
When welding, the fitting is fixed on top of the pipe. The process begins after the welding unit has warmed up to the required temperature. The fitting is put on the mandrel until it stops, which requires some effort. Similarly, at the same time as the fitting is put on, a straight section is inserted into the sleeve. All this must be done as quickly as possible. Initially, the outer size of the pipe is slightly larger than the inner diameter of the sleeve, and the outer diameter of the mandrel is larger than the inner diameter of the fitting (which is why the force is required). During the heating process, the excess layer of the pipe in the fused form protrudes out, forming a grate in the form of a roller. The same happens with the outer layer of the fitting, as a result of which it acquires the diameter of the drone. When you feel that the elements have reached the stop, you must stop pressing, otherwise they will deform. Hold the elements in this position until the end of the process (according to the specified time), then immediately remove them from the nozzle and insert them into each other until they stop. After cooling down, the structure becomes solid and monolithic. To securely fasten the parts, it is necessary to plan the depth of entry of the pipe into the adapter before welding. It should be understood that elements of different sizes are planted at different depths. To determine the required depth, first measure it. If you do not know how to choose the depth, the diameter of the pipe may decrease, or even the pipe may be soldered.
For cutting pipes, special scissors are used, with which you can cut the product at an angle of 90 degrees to its axis. After that, the cut is cleaned with a special device. The order of operations performed during pipeline welding and their correct execution plays a crucial role for the quality of the assembled structure. Before starting the procedure, the surface of the products and attachments must be treated with alcohol. All foreign contamination must be carefully removed, otherwise the Teflon layer may be scratched. The straight section of the pipe must be inserted into the fitting until it stops, leaving no gaps. However, efforts should be proportionate to prevent the narrowing of the diameter and the infusion tube. The use of elements made of polypropylene makes it possible to assemble the installation of any shape, while it remains monolithic and durable, it serves for a long time. During welding, often connected parts overheat. You can find out the required time of heating and cooling of nodes of a certain section from the table below.
The system is attached to building structures by means of special clamping brackets of the appropriate diameter. In this case, the pipes can move along the axis during thermal expansion, avoiding damage.